隨著(zhù)科技的進(jìn)步,世界各國對武器裝備、機械產(chǎn)品的性能要求越來(lái)越高。傳統的碳鋼、鑄鐵等材料已遠遠不能滿(mǎn)足高端裝備對質(zhì)輕、高強、電磁屏蔽等性能需求,因此有色金屬及合金逐漸取代鋼材而成為重要裝備的主體材料,在航天飛行器、智能機器人、高精尖電子儀器設備等領(lǐng)域的應用愈發(fā)廣泛[1-2]。
目前已知的有色金屬有鋁、鎂、鈦、銅、鉛、鋅、鎳、錫、銻、汞等,工業(yè)領(lǐng)域以鋁、鎂、鈦、銅的應用最為廣泛[3]。為提升裝備的機械性能,獲得復合型多功能材料,有色金屬的表面改性處理已成為材料科學(xué)研究的熱點(diǎn),常用的表面改性技術(shù)有電沉積、激光熔覆等。電沉積技術(shù)具有對基體無(wú)損傷、無(wú)熱影響、不改變基體組織等優(yōu)點(diǎn)[4-6]。在有色金屬表面電沉積一層性能與之互補的金屬或合金能夠有效提高材料的綜合性能[7]。
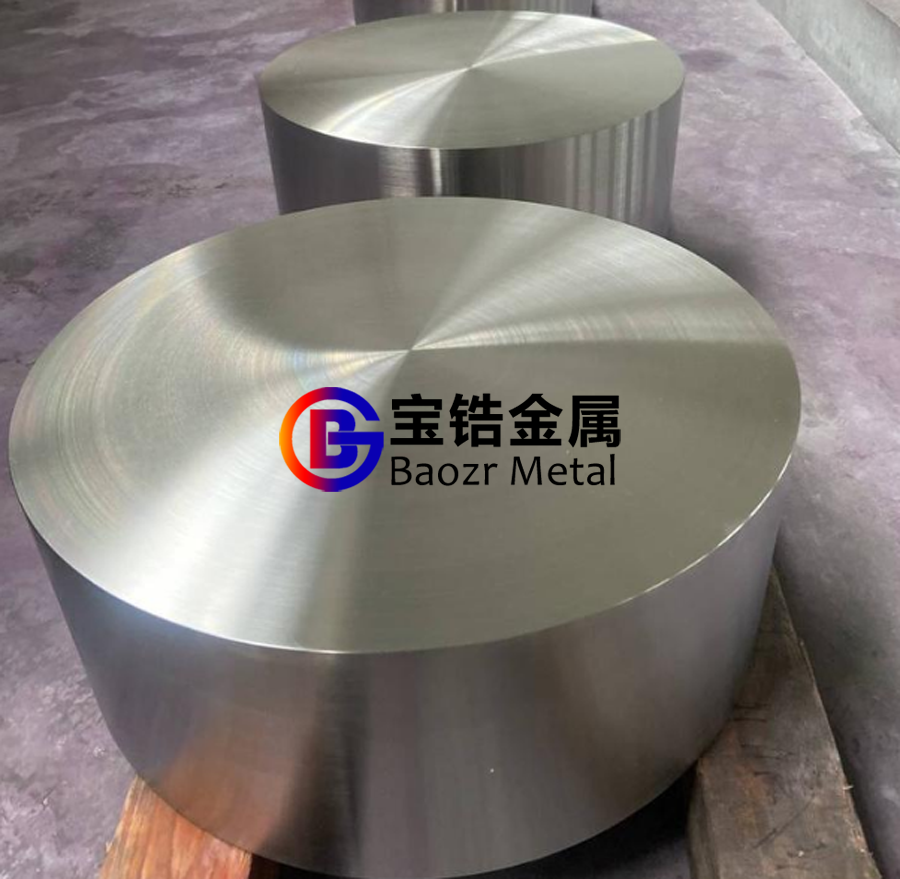
本文針對工業(yè)中常用的有色金屬鋁、鎂、鈦、銅及其合金的水溶液電沉積和離子液體電沉積表面改性技術(shù)的研究進(jìn)展進(jìn)行了總結,為進(jìn)一步研究有色金屬表面電沉積提供參考。
1、電沉積技術(shù)簡(jiǎn)介
1.1電沉積技術(shù)原理
電沉積技術(shù)作為表面工程領(lǐng)域的重要技術(shù),可通過(guò)沉積不同的鍍層來(lái)提高基體材料的耐腐蝕和耐磨損性能,延長(cháng)零件的使用壽命。電沉積還具有裝飾功能,賦予產(chǎn)品平整、光亮的外觀(guān)。電沉積的主要原理是電解液中的金屬離子在外加電源的作用下,通過(guò)電化學(xué)反應沉積至待鍍零件(陰極)表面[8-9]。
1.2離子液體電沉積技術(shù)
目前水溶液電沉積已廣泛應用于工業(yè)生產(chǎn)與科學(xué)研究的各個(gè)領(lǐng)域,具有技術(shù)成熟、基材范圍廣、成本低、生產(chǎn)效率高等優(yōu)勢。隨著(zhù)科技的進(jìn)步,離子液體電沉積技術(shù)逐步發(fā)展起來(lái),并開(kāi)始應用于有色金屬及合金的表面改性處理。相較于傳統水溶液電鍍,離子液體電鍍的研發(fā)時(shí)間晚,尚未形成工業(yè)化規模,但它具有諸多優(yōu)勢,如離子液體中通常不含水,可以避免電沉積過(guò)程中發(fā)生析氫反應,進(jìn)而防止鍍層發(fā)生氫脆現象[10]。離子液體電沉積是采用由有機陽(yáng)離子與無(wú)機或有機陰離子構成的在室溫下呈液態(tài)的有機鹽作為鍍液,將待加工零件作為陰極,高純度目標金屬板作為陽(yáng)極,在外加電源作用下,通過(guò)電子運動(dòng)使目標金屬沉積在待鍍零件表面形成鍍層的過(guò)程。離子液體鍍液一般具有以下優(yōu)點(diǎn):1)沸點(diǎn)低,不易揮發(fā),低蒸汽壓,可用于高真空下的反應;2)具有較高的化學(xué)穩定性和熱穩定性;3)能夠溶解無(wú)機物和高分子有機物;4)綠色無(wú)污染,對環(huán)境友好;5)電化學(xué)窗口寬,導電性能良好[11]。
1.3鍍層種類(lèi)
通過(guò)電沉積可對金屬或非金屬材料進(jìn)行表面改性。根據用途,鍍層可分為防護性鍍層、功能性鍍層和裝飾性鍍層。防護性鍍層主要有Zn、Cd及其合金鍍層,這類(lèi)鍍層通常要進(jìn)一步的鈍化處理,以提高耐腐蝕性能。功能性鍍層主要有硬Cr、Cu、Sn及其合金,可提升基體的表面硬度、導電導熱性、可焊性等性能。裝飾性鍍層主要為Au、Ag、裝飾Cr等,能夠提升基體的美觀(guān)性[12]。此外,還可在金屬或合金鍍液中加入不同類(lèi)型的第二相不溶性顆粒(如碳納米管、石墨烯、Al2O3、SiC等),電沉積獲得綜合性能優(yōu)良的復合鍍層[13]。
2、有色金屬表面電沉積技術(shù)的研究進(jìn)展
2.1鋁及鋁合金
鋁在地球上分布廣、儲量多,比鈦、鎂、鐵的總量還要多,約占地殼的8.2%,其產(chǎn)量在有色金屬中居首位。鋁及其合金具有密度低、比強度高等優(yōu)異特性,被廣泛應用在航空、航天、國防工業(yè)及日常生活中[14]。我國首顆人造衛星“東方紅一號”的外殼就是鋁合金材質(zhì)。鋁合金在美國彈道導彈的用量為30%~50%,阿波羅Ⅱ號飛船的鋁及鋁合金用量占75%,空客和波音公司的飛機用鋁量高達70%,因此鋁被稱(chēng)為“會(huì )飛”的金屬[15-16]。鋁及鋁合金的電負性較強,表面極易氧化形成1~3nm厚的氧化鋁膜,雖然具有一定的耐蝕性,但由于過(guò)薄,在極端條件下反而會(huì )加重鋁的全面腐蝕。鋁的腐蝕多為縫隙腐蝕、點(diǎn)腐蝕、晶間腐蝕、層狀腐蝕等形式[17-18]。因此,提高鋁及鋁合金的耐蝕性、裝飾性、功能性和使用壽命具有重要意義。
相比于其他金屬表面處理工藝,在鋁合金表面電鍍可增強鋁及鋁合金的耐蝕性,有效延長(cháng)其使用壽命。電鍍有著(zhù)操作溫度低的特點(diǎn),能夠使鍍層牢固地與金屬基體結合。雖然電鍍技術(shù)有著(zhù)廣泛應用,但是在鋁合金電鍍前處理過(guò)程中,還存在著(zhù)一些不能忽視的問(wèn)題和不足,如:工藝復雜,操作工序多;鋁合金牌號不同,前處理工藝也不同;產(chǎn)品的合格率很低;前處理溶液使用壽命短;等等。因此要加強鋁及鋁合金電鍍前處理工藝的研究,提高前處理效果。
丁運虎等[19]針對高硅鋁合金電沉積前處理過(guò)程中存在的磷酸根、氫氟酸、重金屬、硝酸、氰化物等物質(zhì)的污染問(wèn)題,開(kāi)發(fā)了環(huán)保的前處理工藝。他們先采用無(wú)磷、低COD(化學(xué)需氧量)體系進(jìn)行除油,接著(zhù)使用無(wú)磷長(cháng)效堿蝕劑進(jìn)行堿蝕,然后采用由雙氧水、酒石酸、檸檬酸和穩定劑組成的溶液除垢,再用自主研發(fā)的無(wú)氰、無(wú)鎳沉鋅液和環(huán)保退鋅液進(jìn)行沉鋅與退鋅,所得沉鋅層孔隙率低至0.1個(gè)/cm2,后續電鍍鎳層結晶細致,結合力良好。
常德華[20]對鋁合金電沉積前處理工藝進(jìn)行了總結和分析,提出了鋁合金鍍前清洗噴淋工藝,即在工件浸入清洗水槽的同時(shí)開(kāi)啟噴頭與超聲設備,進(jìn)而達到高效清洗的目的。他還對浸鋅工藝進(jìn)行了優(yōu)化,避免加工過(guò)程中掛具及其他金屬與鋁合金發(fā)生置換反應,并做好浸鋅過(guò)程的溫度調控,最終使產(chǎn)品的合格率大幅提升。
曾領(lǐng)才等[21]總結了鋁合金表面電鍍處理的優(yōu)缺點(diǎn),對前處理工藝進(jìn)行了優(yōu)化改進(jìn),提出如下工藝流程:脫脂堿蝕二合一→水洗→酸洗→水洗→去灰→水洗→堿性活化→浸鋅(或浸多元合金)→水洗→中性鍍鎳→水洗→電鍍。該工藝適用于多種牌號的鋁及鋁合金電鍍前處理,電鍍層分布均勻、結合力良好。
徐金來(lái)等[22]開(kāi)發(fā)了一套適用于汽車(chē)鋁合金輪轂的電鍍工藝,具體流程為:除蠟→除油→弱堿蝕→沉鋅→預鍍鎳(銅)→鍍高硫鎳→鍍光亮鎳→鎳封→鍍鉻。杜中德等[23]通過(guò)脈沖電沉積Ni–W合金對泡沫鋁進(jìn)行表面改性處理,準靜態(tài)壓縮測試結果表明,鍍Ni–W合金泡沫鋁的峰值應力比未鍍和鍍Ni泡沫鋁分別高了45%和10%,耐蝕性也最優(yōu)。
哈爾濱工業(yè)大學(xué)的張建清[24]針對鋁合金電鍍傳統浸鋅前處理存在的工序復雜和環(huán)保問(wèn)題(如使用劇毒的氰化物),采用1?丁基?3?甲基咪唑三氟甲烷磺酸鹽或1?乙基?3?甲基咪唑三氟甲烷磺酸鹽離子液體與乙醇組成的混合溶劑體系,直接在鋁合金表面恒流電沉積Cu–Zn合金。所得Cu–Zn合金鍍層致密平整,結合力良好,耐蝕性?xún)?yōu)于浸鋅層。該工藝符合綠色環(huán)保的要求,有望替代有毒的氰化物浸鋅前處理工藝。
電沉積是目前解決鋁及鋁合金易腐蝕、耐磨性差等問(wèn)題的主要手段。而鋁合金表面電沉積的主要問(wèn)題在于增強基體與鍍層的結合力,因此前處理是鋁合金電鍍研究的重點(diǎn)之一,應引起重視。
2.2鎂及鎂合金
鎂是銀白色的超輕有色金屬,密度為1.74g/m3,在地殼中的占比約為1.93%。將Zn、Si、Al等元素添加在鎂中即可形成鎂基合金[25]。鎂合金的比強度高于鋁合金和普通鋼材,具有良好的切削加工性、熱傳導性、空間穩定性、電磁屏蔽性、阻尼性等性能,早期較多用于航空航天領(lǐng)域,近年來(lái)在汽車(chē)、光學(xué)儀器、電子、通信、軍工等方面的應用增多。但鎂及鎂合金的化學(xué)性質(zhì)非?;顫?,在酸性溶液和中性鹽溶液中都容易發(fā)生腐蝕[26-27]。因此,在鎂合金表面電沉積防護鍍層,能夠在不改變其輕量化優(yōu)點(diǎn)的前提下,提升其耐腐蝕性能,延長(cháng)使用壽命,對于拓寬鎂合金的應用具有重要意義。
鎂合金活潑的化學(xué)性質(zhì)使其很難直接進(jìn)行電鍍或化學(xué)鍍,因此適當的前處理工藝極其重要。邢倩[28]在A(yíng)Z91D鎂合金電鍍銅前分別進(jìn)行化學(xué)鍍鎳和浸鋅,并優(yōu)化了這兩種前處理方法的工藝流程和參數。
然而無(wú)論采用哪種前處理工藝,酸洗活化都極其重要。采用浸鋅法時(shí),較佳的酸洗活化工藝條件為:
C2H2O4·2H2O(草酸)12g/L,NaF50g/L,溫度25~35°C,時(shí)間1~5min。變溫浸鋅優(yōu)于恒溫浸鋅,較優(yōu)的浸鋅工藝條件為:ZnSO4·7H2O30g/L,Na2P2O7120g/L,NaF3g/L,Na2CO35g/L,溫度從30°C升至40°C,pH10.2~10.4,10~15min。采用化學(xué)鍍鎳法時(shí),尤其要控制好活化過(guò)程的析氫反應,較佳的工藝流程為:電解拋光→熱水洗→冷水洗→電解除油→熱水洗→冷水洗→酸洗(硫酸24mL/L,硝酸78mL/L,室溫,時(shí)間1~2min)→熱水洗→冷水洗→活化(HF375mL/L,室溫,時(shí)間10~20s)→冷水洗→化學(xué)鍍鎳。采用化學(xué)鍍鎳前處理時(shí),后續電鍍銅層孔隙率低,結合力良好,表面均勻、光亮。
房文靜[29]對比分析了AZ91D鎂合金表面脈沖電沉積鎳和直流電沉積鎳的性能,發(fā)現采用兩種工藝均可在A(yíng)Z91D鎂合金表面獲得均勻的Ni鍍層,并且結合力都合格,但直流電鍍鎳層的耐蝕性更好,電流效率更高。
賀嚴東[30]以1?丁基?4?甲基咪唑氯鹽和AlC13制備的離子液體(BMIC-AlCl3)作為電解液,研究并優(yōu)化了鎂合金浸鋅及其在離子液體電沉積Al的工藝。結果表明,所得Al鍍層均勻平整,與基體間的結合強度達到10.7MPa,耐蝕性良好。
楊海燕等[31]用酸性AlCl3?EMImCl(1–甲基?3?乙基咪唑鹽酸鹽)離子液體在A(yíng)Z91D鎂合金表面進(jìn)行電鍍鋁,研究了不同機械打磨方式及鍍液中水含量對Al鍍層性能的影響。結果表明,AZ91D鎂合金經(jīng)細砂(粒度W14)以畫(huà)圓方式打磨及清洗后,可在干燥的AlCl3?EMImCl離子液體中電鍍得到均勻致密、結合力強和耐蝕性良好的Al鍍層。
常慶明等[32]通過(guò)正交試驗得到鎂合金鍍前的較佳酸洗工藝:250g/LCrO3+20mL/L濃硝酸,室溫,時(shí)間30s。在該較優(yōu)條件下酸洗后,再用200mL/LH3PO4+100g/LNH4HF2溶液在室溫下活化60s,接著(zhù)用以ZnSO4·7H2O和K4P2O7·3H2O為主成分的焦磷酸鹽浸鋅液浸漬150s,顯著(zhù)提高了后續電鍍鎳層的結合力及耐蝕性。
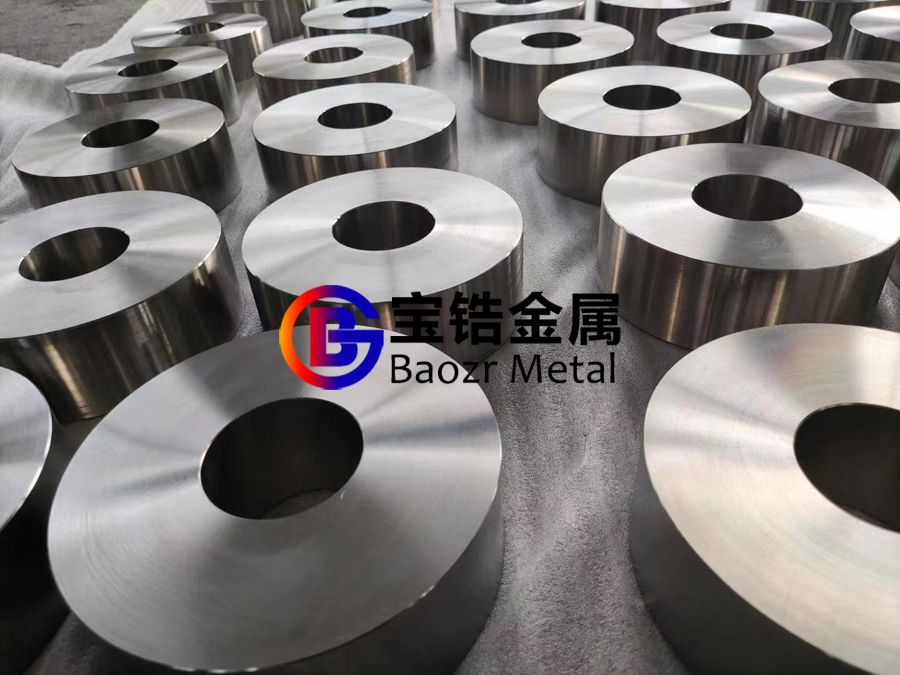
鎂及鎂合金表面極易形成惰性氧化膜,影響后續電鍍的順利進(jìn)行及鍍層結合力,因此在電鍍前應去除表面氧化膜。目前鎂合金較常用的電鍍前處理方法為浸鋅和化學(xué)鍍鎳。浸鋅過(guò)程需精確控制,直接影響鍍層品質(zhì)?;瘜W(xué)鍍鎳面臨的主要問(wèn)題是鍍液呈酸性,會(huì )腐蝕鎂合金基體。因此,目前鎂合金電沉積的工業(yè)化應用范圍依然有限,雖然有不少新型前處理技術(shù)被開(kāi)發(fā),但多數還停留在實(shí)驗室階段,缺少工程化應用驗證,故急需開(kāi)發(fā)一種非酸性、適應性強、使用壽命長(cháng)、無(wú)污染的前處理工藝。
2.3鈦及鈦合金
鈦合金被稱(chēng)為“太空金屬”,具有密度小,耐蝕性和耐熱性好、比強度高,以及生物相容性好等優(yōu)點(diǎn),是航空航天、汽車(chē)制造等領(lǐng)域不可或缺的有色金屬材料[33]。但鈦及鈦合金的硬度較低,耐磨性差,在加工過(guò)程中易粘著(zhù),極大地限制了其應用。對鈦合金表面電沉積適宜的鍍層能夠提高其硬度、耐磨性等性能,是解決鈦合金在特殊工況環(huán)境中存在缺陷問(wèn)題的有效途徑之一[33-34]。
鈦合金在許多介質(zhì)中都容易發(fā)生自鈍化,不利于獲得結合力良好的鍍層。針對此問(wèn)題,于海等[35]先對鈦合金表面進(jìn)行活化和氫化處理,再電鍍銅,具體工藝流程為:噴砂→活化(鹽酸45mL/L,氫氟酸27mL/L,室溫,時(shí)間30~45s)→氫化處理(硫酸500g/L,鹽酸210g/L,室溫,時(shí)間30~60min)→電鍍銅→鈍化→熱處理。所得Cu鍍層的結合力、焊接性、導電性及耐蝕性均良好。該工藝已成功應用在國內某先進(jìn)型號戰機零部件上。
付強[36]先在TC4鈦合金油套管表面預鍍Ni中間層,280°C熱處理后再沖擊鍍Ni,最后電鍍Cu–Sn合金(配方為:氰化亞銅30~40g/L,錫酸鈉35~45g/L,游離氰化鈉18~25g/L,氫氧化鈉6~10g/L)。所得Cu–Sn合金鍍層具有優(yōu)異的結合力、抗粘扣性和耐蝕性。該研究有助于鈦合金油套管產(chǎn)品在油氣田復雜腐蝕環(huán)境中的推廣應用。
袁永超等[37]對比了TC4鈦合金鍍前活化、活化+化學(xué)預鍍鎳和陽(yáng)極氧化對電鍍Ni–P合金鍍層顯微硬度、結合力、表面粗糙度和微觀(guān)形貌的影響。結果表明,前處理工藝對鍍層性能的影響較大,較佳的前處理工藝為“活化+預鍍Ni”。其中活化工藝條件為:NaBF440g/L,NaNO360g/L,溫度80°C,時(shí)間10min;預鍍Ni工藝條件為:NiSO4·6H2O50g/L,CH3COONa13g/L,NaH2PO2·H2O25g/L,NH4Cl10g/L,pH5,時(shí)間5min。所制備的Ni–P合金鍍層均勻、平整而致密,結合力好,顯微硬度為625HV,表面粗糙度Ra為0.626μm。
趙立才等[38]采用類(lèi)似工藝對TC2鈦合金進(jìn)行前處理,再電沉積乳白鉻中間層,真空退火處理后浸于硬鉻鍍液中預熱2~5min,接著(zhù)在30~40A/dm2下活化20~60s,最后電沉積硬鉻層。結果表明,所得的雙層鍍鉻層與鈦合金基體之間結合良好,顯微硬度達750HV,耐磨性?xún)?yōu)良。鈦及鈦合金電鍍的主要難點(diǎn)在于基體與鍍層之間的結合力較差。因為鈦屬于熱力學(xué)不穩定金屬,表面極易形成一層穩定的鈍化膜。鈦合金表面防護處理的常規方法有轉化膜法、金屬底層法、避免氧介質(zhì)法等,但在實(shí)際工程應用中這些方法多少都面臨工藝繁瑣、生產(chǎn)成本高等問(wèn)題,因此開(kāi)發(fā)鈦及鈦合金電沉積新工藝具有重要意義。
2.4銅及銅合金
銅及銅合金具有良好的導電、導熱等性能,被廣泛應用于武器裝備、航空航天、艦船制造等領(lǐng)域[39]。但銅及銅合金的硬度低,耐磨性差,不能直接用于磨損沖擊環(huán)境,而且在一些高腐蝕環(huán)境中的耐蝕性也明顯不足[40]。因此對銅及銅合金進(jìn)行表面強化,提高其綜合性能,成為了目前的研究熱點(diǎn)。
劉建等[41]采用亞硫酸鹽體系在黃銅和紫銅表面電沉積Au–Cu?Ni合金,所得Au?Cu?Ni合金鍍層光亮、致密,耐蝕性和耐磨性良好,顯微硬度為297HV0.025,電阻率為1.84μ?·cm,接觸電阻變化較穩定,能夠滿(mǎn)足滑動(dòng)電連接器高導電、高耐磨的要求。
馬久明等[42]采用氨基磺酸鹽體系在銅基板表面電沉積Ni–rGO(還原氧化石墨烯)復合鍍層,與純Ni鍍層相比。Ni–rGo復合鍍層的Ni晶粒更細小,石墨烯片均勻分布于鎳晶粒之間,有少量鎳晶粒被石墨烯片包裹填充至鍍層孔洞處。在廣東地區的近海域海水中浸泡60d后,Ni–rGO復合鍍層表面保持平整,無(wú)明顯的孔洞,說(shuō)明該復合鍍層能夠有效阻擋海水對銅基體的腐蝕。
為提高銅接地材料在弱酸性(酸性)土壤介質(zhì)中的耐蝕性,方晨旭[43]采用脈沖電鍍和化學(xué)鍍兩種方法在銅表面制備了幾種鎳基合金(如Ni?P、Ni?W?P和Ni?Sn?P)鍍層,通過(guò)電化學(xué)阻抗譜、動(dòng)電位極化曲線(xiàn)測試和模擬地下銅線(xiàn)腐蝕環(huán)境試驗分析了它們在不同弱酸性環(huán)境下的耐腐蝕性能。結果表明,這些鎳基合金鍍層相對于銅基體而言都屬于陽(yáng)極性鍍層,在弱酸性土壤介質(zhì)中表現出優(yōu)于銅基體的耐蝕性,可應用于接地銅材的表面改性處理。
王剛[9]在純銅表面電沉積Ni?Co?Fe合金鍍層,鍍液組成為:NiSO4·6H2O220g/L,NiCl2·6H2O40g/L,CoSO4·7H2O20g/L,FeSO4·7H2O10g/L,H3BO350g/L,檸檬酸鈉40g/L。在研究了不同因素對Ni?Co?Fe合金鍍層性能的影響后得到較佳的電沉積工藝條件為:pH4,溫度55℃,電流密度4A/dm2。所得鍍層致密、晶粒細小,Co、Ni和Fe的質(zhì)量分數分別為31.5%、49.7%和18.5%,結合力良好,顯微硬度達到818.77HV,有望成為代鉻鍍層。
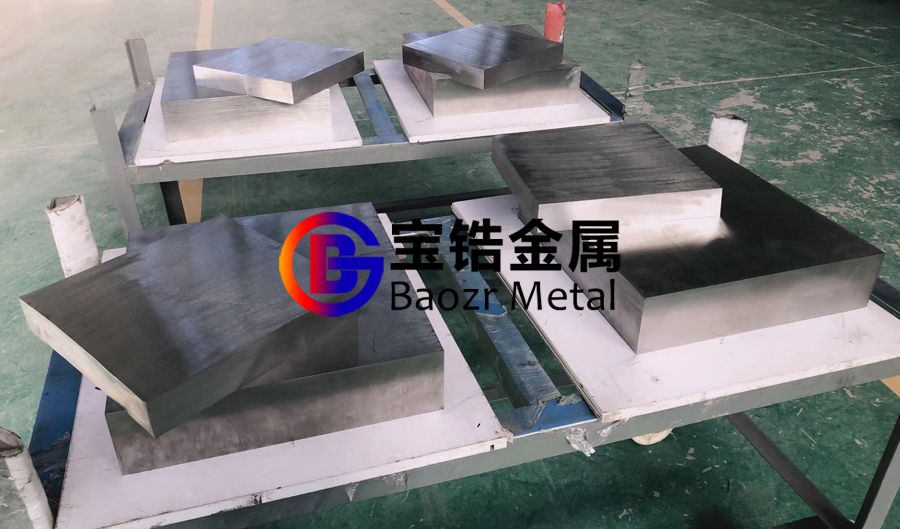
隨著(zhù)人們環(huán)保意識的逐漸提升,離子液體電沉積技術(shù)目前正逐漸應用于銅基體的表面改性。
Survilien?等[44]采用含0.36mol/LCrCl3·6H2O的[BMIM]BF4(1?丁基?3?甲基咪唑四氟硼酸鹽)離子液體,于密閉充氮環(huán)境下在銅表面電沉積得到厚度為1~2μm的非晶態(tài)黑Cr鍍層,但其耐蝕性和硬度都不如晶態(tài)Cr鍍層,并存在微裂紋、瘤體等缺陷。李晨[45]采用含0.5mol/LCrCl3·6H2O的[EMIM]HSO4(1?丁基?3?甲基咪唑硫氫酸鹽)離子液體在銅片表面電沉積Cr,通過(guò)研究不同因素對電沉積速率的影響,得到了較優(yōu)工藝條件為:溫度50℃,電流密度50mA/cm2,時(shí)間50min。所得Cr鍍層厚度為9.2μm,均勻致密,呈晶態(tài)結構,耐蝕性?xún)?yōu)于[BMIM]BF4體系Cr鍍層。
銅及銅合金材料易氧化、腐蝕等缺點(diǎn)嚴重制約著(zhù)其在高端裝備領(lǐng)域的應用。在銅及銅合金表面電沉積既保留了其優(yōu)良的導電、導熱性能,還提高了其抗氧化、耐腐蝕等性能,具有很好的應用前景。
3、結語(yǔ)
隨著(zhù)科技的發(fā)展,高端精密裝備對有色金屬的需求逐漸增加,多功能金屬材料將會(huì )成為未來(lái)航空航天、電子科技、大型裝備的主流材料。利用電沉積技術(shù)在有色金屬表面制備功能多樣、性能可控的金屬鍍層是材料表面工程領(lǐng)域的研究熱點(diǎn)。國內的傳統水溶液電沉積技術(shù)已較為成熟,但一些新型離子液體電沉積工藝仍存在很多不足。加快推進(jìn)離子液體電沉積技術(shù)的研究及工業(yè)化應用,不僅對于減少環(huán)境污染,避免氫脆隱患及提升產(chǎn)品可靠性具有積極作用,而且對于提升我國高端制造能力,促進(jìn)我國由制造大國向制造強國轉變具有重要意義。
參考文獻:
[1] 肖紀美, 曹楚南.材料腐蝕學(xué)原理[M].北京: 化學(xué)工業(yè)出版社, 2002.
XIAO J M, CAO C N.Principle of Material Corrosion [M].Beijing: Chemical Industry Press, 2002.
[2] 劉二勇, 曾志翔, 趙文杰.海水環(huán)境中金屬材料腐蝕磨損及耐磨防腐一體化技術(shù)的研究進(jìn)展[J].表面技術(shù), 2017, 46 (11): 149-157.
LIU E Y, ZENG Z X, ZHAO W J.Corrosion wear and integrated anti-wear & anti-corrosion technology metallic materials in seawater [J].Surface Technology, 2017, 46 (11): 149-157.
[3] 李多.紫銅在人工海水中的沖刷腐蝕行為研究[D].哈爾濱: 哈爾濱工程大學(xué), 2013.
LI D.Erosion-corrosion behavior of copper in artificial seawater [D].Harbin: Harbin Engineering University, 2013.
[4] 路晨, 王海人, 屈鈞娥, 等.碳材料在金屬防腐蝕中的應用研究進(jìn)展[J].腐蝕科學(xué)與防護技術(shù), 2014, 26 (3): 254-258.
LU C, WANG H R, QU J E, et al.Progress on research application of carbon materials for corrosion protection of metallic materials [J].Corrosion Science and Protection Technology, 2014, 26 (3): 254-258.
[5] 王一雍, 孫爭光, 金輝, 等.結晶器銅板表面激光熔覆 Ni–Co–Al2O 3 復合涂層的微觀(guān)組織及性能[J].功能材料, 2015, 46 (20): 20148-20152.
WANG Y Y, SUN Z G, JIN H, et al.Microstructure and property of Ni/Co/Al2O 3 laser cladding layer on the surface of mold copper plate [J].Journal of Functional Materials, 2015, 46 (20): 20148-20152.
[6] 魏曉冬.電沉積制備鋁鈦合金的研究[D].沈陽(yáng): 沈陽(yáng)大學(xué), 2019.
WEI X D.Study on preparation of Al–Ti alloy by electrodeposition [D].Shenyang: Shenyang University, 2019.
[7] 徐濱士, 譚俊, 陳建敏.表面工程領(lǐng)域科學(xué)技術(shù)發(fā)展[J].中國表面工程, 2011, 24 (2): 1-12.
XU B S, TAN J, CHEN J M.Science and technology development of surface engineering [J].China Surface Engineering, 2011, 24 (2): 1-12.
[8] 屠振密.電鍍合金原理與工藝[M].北京: 國防工業(yè)出版社, 1993.
TU Z M.Principle and Process of Alloy Electroplating [M].Beijing: National Defense Industry Press, 1993.
[9] 王剛.銅表面電沉積 Ni–Co–Fe 合金層工藝及性能研究[D].淄博: 山東理工大學(xué), 2015.
WANG G.The studies of electrodeposition and properties of Ni–Co–Fe alloys on copper [D].Zibo: Shandong University of Technology, 2015.
[10] 薛東朋, 徐霸津, 陳益明, 等.AlCl 3 -EMIC 離子液體電沉積光亮 Al 和 Al–Mn 鍍層[J].化工學(xué)報, 2015, 66 (增刊 1): 282-286.
XUE D P, XU B J, CHEN Y M, et al.Electrodeposition of bright Al and Al–Mn coatings from AlCl 3 -EMIC ionic liquid [J].CIESC Journal, 2015, 66 (Suppl.1): 282-286.
[11] 周君, 周淑梅.離子液體中低溫制備鋁技術(shù)研究進(jìn)展[J].上?;? 2017, 42 (2): 34-38.
ZHOU J, ZHOU S M.Technical progress of aluminum preparation at low temperature in ionic liquids [J].Shanghai Chemical Industry, 2017, 42 (2):34-38.
[12] ELIAS L, HEGDE A C.Synthesis of Ni–W–graphene oxide composite coating for alkaline hydrogen production [J].Materials Today: Proceedings,2018, 5 (1, Part 3): 3078-3083.
[13] 丁小龍, 胡振峰, 金國, 等.輕質(zhì)碳材料應用于復合鍍的研究現狀[J].電鍍與涂飾, 2017, 36 (11): 604-608.
DING X L, HU Z F, JIN G, et al.Research status of light-weight carbon materials applied to composite plating [J].Electroplating & Finishing, 2017,36 (11): 604-608.
[14] 田榮璋, 王祝堂.鋁合金及其加工手冊[M].2 版.長(cháng)沙: 中南大學(xué)出版社, 2000.
TIAN R Z, WANG Z T.Aluminum Alloys and their Processing Manual [M].2nd ed.Changsha: Central South University Press, 2000.
[15] 王孟君, 黃電源, 姜海濤.汽車(chē)用鋁合金的研究進(jìn)展[J].金屬熱處理, 2006, 31 (9): 34-38.
WANG M J, HUANG D Y, JIANG H T.Research progress of aluminium alloys for the automotive industry [J].Heat Treatment of Metals, 2006, 31 (9):34-38.
[16] 畢晨, 劉定富, 曾慶雨.2A12 鋁合金化學(xué)鍍鎳前處理工藝研究[J].貴州科學(xué), 2016, 34 (3): 88-92.
BI C, LIU D F, ZENG Q Y.A study on pretreatment process of electroless nickel plating on 2A12 Aluminum alloy [J].Guizhou Science, 2016, 34 (3):88-92.
[17] 朱祖芳.鋁合金陽(yáng)極氧化與表面處理技術(shù)[M].北京: 化學(xué)工業(yè)出版社, 2004.
ZHU Z F.Technology of Anodic Oxidation and Surface Treatment on Aluminum Alloys [M].Beijing: Chemical Industry Press, 2004.
[18] 周鼎華.鋁合金表面處理技術(shù)新進(jìn)展[J].熱處理技術(shù)和裝備, 2006, 27 (4): 10-15.
ZHOU D H.Recently progress on surface treatment technology of aluminum alloys [J].Heat Treatment Technology and Equipment, 2006, 27 (4):10-15.
[19] 丁運虎, 黃興林, 鄧華才, 等.高硅鋁合金電鍍環(huán)保前處理技術(shù)研究[J].材料保護, 2017, 50 (4): 55-57, 72.
DING Y H, HUANG X L, DENG H C, et al.Environmentally friendly pretreatment technology on high-silicon aluminum alloy before electroplating [J].Materials Protection, 2017, 50 (4): 55-57, 72.
[20] 常德華.鋁合金電鍍前處理技術(shù)探究[J].冶金與材料, 2022, 42 (1): 67-68.
CHANG D H.Study on pretreatment technology for electroplating on aluminum alloy [J].Metallurgy and Materials, 2002, 42 (1): 67-68.
[21] 曾領(lǐng)才, 文偉, 謝輝.鋁及鋁合金電鍍前處理工藝的改進(jìn)[J].電鍍與涂飾, 2012, 31 (3): 15-17.
ZENG L C, WEN W, XIE H.Improvement of pretreatment process of aluminum and its alloys before plating [J].Electroplating & Finishing, 2012,
31 (3): 15-17.
[22] 徐金來(lái), 趙國鵬, 胡耀紅, 等.鋁輪轂電鍍工藝應用[J].電鍍與涂飾, 2009, 28 (1): 7-9.
XU J L, ZHAO G P, HU Y H, et al.Application of electroplating process for aluminum wheel hub [J].Electroplating & Finishing, 2009, 28 (1): 7-9.
[23] 杜中德, 劉歡, 沈浩田, 等.泡沫鋁表面 Ni–W 共沉積及性能研究[J].表面技術(shù), 2020, 49 (10): 233-238.
DU Z D, LIU H, SHEN H T, et al.Ni–W co-deposition and property of closed cell aluminum foam [J].Surface Technology, 2020, 49 (10): 233-238.
[24] 張建清.鋁合金表面離子液體電沉積 Cu–Zn 合金過(guò)渡層的研究[D].哈爾濱: 哈爾濱工業(yè)大學(xué), 2019.
ZHANG J Q.Study on electrodeposition of Cu–Zn alloy transition layer from ionic liquid on aluminum alloy [D].Harbin: Harbin Institute of Technology, 2019.
[25] 安茂忠.電鍍理論與技術(shù)[M].哈爾濱: 哈爾濱工業(yè)大學(xué)出版社, 2004.
AN M Z.Electroplating Theory and Technology [M].Harbin: Harbin Institute of Technology Press, 2004.
[26] 劉貴立.鎂合金電子結構與腐蝕特性研究[J].物理學(xué)報, 2010, 59 (4): 2708-2713.
LIU G L.Electronic structure and corrosion character of Mg alloys [J].Acta Physica Sinica, 2010, 59 (4): 2708-2713.
[27] NIU L Y, JIANG Z H, LI G Y, et al.A study and application of zinc phosphate coating on AZ91D magnesium alloy [J].Surface and Coating Technology, 2006, 200 (9): 3021-3026.
[28] 邢倩.AZ91D 鎂合金電鍍前處理工藝的研究[D].大連: 遼寧師范大學(xué), 2011.
XING Q.The study of electroplating pretreatment on AZ91D magnesium alloy [D].Dalian: Liaoning Normal University, 2011.
[29] 房文靜.AZ91D 鎂合金電鍍鎳及其耐蝕性能研究[D].湘潭: 湘潭大學(xué), 2017.
FANG W J.Study on corrosion resistance of AZ91D magnesium alloy by electroless nickel plating [D].Xiangtan: Xiangtan University, 2017.
[30] 賀嚴東.離子液體中鎂合金表面電沉積鋁工藝研究[D].哈爾濱: 哈爾濱工程大學(xué), 2019.
HE Y D.Study on electrodeposition of Al on magnesium alloy surface in ionic liquid [D].Harbin: Harbin Engineering University, 2019.
[31] 楊海燕, 郭興伍, 吳國華, 等.AZ91D 鎂合金在 A1Cl 3 –EMI m Cl 離子液體中電鍍 Al 研究[C] // 2009 年全國電子電鍍及表面處理學(xué)術(shù)交流會(huì )論文集.[出版地不詳: 出版者不詳], 2009: 267-271.
YANG H Y, GUO X W, WU G H, et al.Electroplating of Al onto AZ91D Mg alloy from AlCl 3 –EMI m Cl ionic liquid [C] // Proceedings of National Academic Exchange Conference on Electronic Electroplating and Surface Treatment 2009.[S.l.: s.n.], 2009: 267-271.
[32] 常慶明, 張旭, 付至祥, 等.AZ91D 鎂合金電鍍前處理工藝研究[J].電鍍與涂飾, 2021, 40 (3): 202-207.
CHANG Q M, ZHANG X, FU Z X, et al.Study on pretreatment of AZ91D magnesium alloy before electroplating [J].Electroplating & Finishing,2021, 40 (3): 202-207.
[33] 金和喜, 魏克湘, 李建明, 等.航空用鈦合金研究進(jìn)展[J].中國有色金屬學(xué)報, 2015, 25 (2): 280-292.
JIN H X, WEI K X, LI J M, et al.Research development of titanium alloy in aerospace industry [J].The Chinese Journal of Nonferrous Metals, 2015,25 (2): 280-292.
[34] 馮秋元, 郭佳林, 李蒙, 等.鈦合金電鍍鉻研究現狀及應用[J].材料保護, 2018, 51 (10): 109-113.
FENG Q Y, GUO J L, LI M, et al.Research status and application of electroplating chromium on titanium alloy [J].Materials Protection, 2018, 51 (10):109-113.
[35] 于海, 李云飛, 王志煜, 等.TC2 鈦合金電鍍銅的應用[J].腐蝕與防護, 2015, 36 (5): 432-434.
YU H, LI Y F, WANG Z Y, et al.Application of plating copper on titanium alloy TC2 [J].Corrosion & Protection, 2015, 36 (5): 432-434.
[36] 付強.TC4 鈦合金接箍電鍍銅錫合金工藝[J].電鍍與涂飾, 2019, 38 (19): 1042-1044.
FU Q.Process for electroplating copper–tin alloy on TC4 titanium alloy couplings [J].Electroplating & Finishing, 2019, 38 (19): 1042-1044.
[37] 袁永超, 趙旭升.預處理工藝對鈦合金電鍍鎳?磷合金的影響[J].電鍍與涂飾, 2020, 39 (9): 536-539.
YUAN Y C, ZHAO X S.Effects of different pretreatment processes on electroplating of nickel–phosphorus alloy on titanium alloy [J].Electroplating &Finishing, 2020, 39 (9): 536-539.
[38] 趙立才, 高晶, 沙春鵬.TC2 鈦合金表面電鍍雙層鉻工藝[J].電鍍與涂飾, 2014, 33 (21): 919-921.
ZHAO L C, GAO J, SHA C P.Process for plating double-layer chromium coating on TC2 titanium alloy [J].Electroplating & Finishing, 2014, 33 (21):919-921.
[39] 劉海云, 馮斌, 徐松, 等.不同鍍層對銅接地線(xiàn)在弱酸性介質(zhì)中耐蝕性的影響[J].電鍍與涂飾, 2013, 32 (9): 54-57.
LIU H Y, FENG B, XU S, et al.Influence of different coatings on corrosion resistance of copper ground wire under weakly acidic environment [J].Electroplating & Finishing, 2013, 32 (9): 54-57.
[40] 王瑞.Ni–Cu–P 鍍層制備及稀土化合物對其腐蝕性能影響[D].哈爾濱: 哈爾濱工程大學(xué), 2013.
WANG R.The synthesization of Ni–Cu–P coating and the effect of RE on its corrosion property [D].Harbin: Harbin Engineering University, 2013.
[41] 劉建, 陳志全, 王釗.Au–Cu–Ni 合金在銅基材表面的無(wú)氰電鍍[J].貴金屬, 2018, 39 (1): 47-50.
LIU J, CHEN Z Q, WANG Z.Non-cyanide electroplating of gold–copper–nickel alloy on surface of copper base [J].Precious Metals, 2018, 39 (1):47-50.
[42] 馬久明, 宋士虎, 冼明锏, 等.銅表面鎳?石墨烯的電沉積制備及耐腐蝕性能[J].華南師范大學(xué)學(xué)報(自然科學(xué)版), 2020, 52 (4): 43-49.
MA J M, SONG S H, XIAN M C, et al.Preparation and corrosion resistance of Ni–graphene on copper surface by electrodeposition [J].Journal of South China Normal University (Natural Science Edition), 2019, 52 (4): 43-49.
[43] 方晨旭.銅表面鎳基多元合金鍍層的制備與耐蝕性研究[D].長(cháng)沙: 湖南大學(xué), 2015.
FANG C X.The study of preparation and anti-corrosion performance of nickel-base multielement alloy coatings on Cu substrate [D].Changsha:Hunan University, 2015.
[44] SURVILIEN? S, EUGéNIO S, VILAR R.Chromium electrodeposition from [BMIm][BF 4 ] ionic liquid [J].Journal of Applied Electrochemistry,2011, 41 (1): 107-114.
[45] 李晨.1-乙基-3-甲基咪唑類(lèi)離子液體三價(jià)鉻電沉積鉻鍍層的研究[D].株洲: 湖南工業(yè)大學(xué), 2015.
LI C.Study on electrodeposition of chromium coatings based on Cr(III) bath using 1-ethyl-3-methylimidazole ionic liquid [D].Zhuzhou: Hunan University of Technology, 2015.
相關(guān)鏈接