前言
航空渦輪發(fā)動(dòng)機的壓氣機(含風(fēng)扇+壓氣機)承擔為發(fā)動(dòng)機提供持續、穩定、大流量空氣的任務(wù)。壓氣機被渦輪轉子高速驅動(dòng),旋轉時(shí)在壓氣機葉片的進(jìn)/排氣邊形成空氣壓差從而產(chǎn)生推力,而葉片通過(guò)燕尾型榫槽聯(lián)結于輪盤(pán)[1]。壓氣機輪盤(pán)承受自身離心載荷,以及葉片氣動(dòng)+離心作用的復合載荷。若再考慮壓縮空氣的溫升、燃燒室部件傳熱,則情況更復雜[2]。
由此可知:壓氣機輪盤(pán)的熱力耦合載荷情況復雜,對輪盤(pán)選材、設計、制造過(guò)程均提出極高要求。鈦合金因其比強度高,耐蝕性好,300℃~600℃溫度區間持久、抗蠕變性能優(yōu)良,因而成為航空發(fā)動(dòng)機壓氣機盤(pán)的首選材料,目前先進(jìn)燃氣渦輪發(fā)動(dòng)機壓氣機盤(pán)幾乎均選用鈦合金材料[3]。
壓氣機盤(pán)鍛件屬于大型盤(pán)類(lèi)鍛件,合金鑄錠經(jīng)過(guò)開(kāi)坯鍛造(β轉變溫度以上,歷經(jīng)3~5火次),快鍛與精鍛(α+β雙相區,歷經(jīng)4~6火次)后制成大規格棒材(?180mm以上)[4],隨后大規格棒材經(jīng)過(guò)坯料的鍛錘壓鍛及最終的壓力機模鍛而成盤(pán)鍛件,熱工藝流程繁多,而鈦合金鍛造過(guò)程同時(shí)發(fā)生組織轉變與再結晶,因此鍛件毛坯質(zhì)量是決定產(chǎn)品質(zhì)量的基礎,而制定科學(xué)標準是毛坯質(zhì)量的重要保障。
然而,由于鍛件標準體現設計員對零件承載類(lèi)型、受力狀況、材料組織、熱處理與性能等諸多方面的全面要求,對設計人員知識、經(jīng)驗要求較高,我國航空發(fā)動(dòng)機部件設計人員大多從院校畢業(yè)后即從事設計工作,缺乏生產(chǎn)現場(chǎng)實(shí)踐經(jīng)驗,導致在擬定鍛件標準過(guò)程中硬搬國外標準,或套用普通鈦合金模鍛件通用標準的現象,致使發(fā)動(dòng)機產(chǎn)品質(zhì)量存在安全隱患?;谏鲜銮闆r,有必要選擇典型的壓氣機盤(pán)鍛件標準,結合實(shí)物檢測數據進(jìn)行技術(shù)細節的對比與分析,從而幫助厘清思路,明辨技術(shù)細節,積累設計經(jīng)驗,加強質(zhì)量管控水平,提高產(chǎn)品質(zhì)量。
1、實(shí)驗材料與方法
1.1實(shí)驗材料
選擇XX7渦噴發(fā)動(dòng)機的TC11合金制盤(pán)鍛件(爐號351-120598)、XX17渦扇發(fā)動(dòng)機的TC8-1合金制盤(pán)鍛件(爐號TC8-1-20122238),以及XX13渦扇發(fā)動(dòng)機的TC25合金制盤(pán)鍛件(爐號241-0007)為對象。對比三者盤(pán)鍛件標準的取樣、測試項目、性能要求,并與實(shí)物狀態(tài)測試數值比較,最終獲得實(shí)驗結論。
1.2化學(xué)成分
TC11鈦合金名義成分為T(mén)i-6.5Al-1.5Zr-3Mo-0.25Si,TC25為T(mén)i-6.7Al-1.5Sn-1.5Zr-2Mo-1W-0.25Si,TC8-1為T(mén)i-6.3Al-1Sn-1Zr-3.3Mo-0.18Si。
根據Al當量[Al]與Mo當量[Mo]的計算公式[5],將三種鈦合金的計算結果及β轉變溫度列于表1。
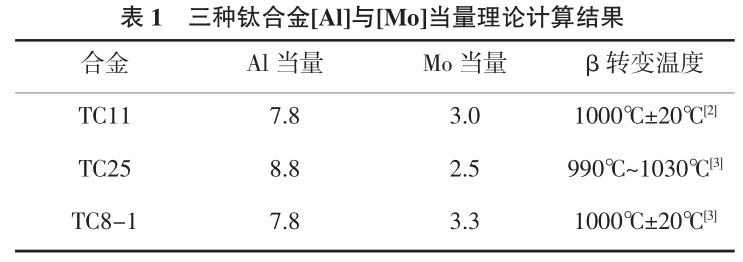
1.3輪盤(pán)承載
以圖1說(shuō)明壓氣機盤(pán)工作過(guò)程承受的復雜的熱—載荷耦合作用:①輪盤(pán)+葉片的高速旋轉,產(chǎn)生徑向與周向離心載荷,疊加輪緣—輪轂溫度梯度形成的熱應力,導致輪緣芯部呈三向應力狀態(tài)。其中壁厚較薄的幅板與輪轂部位徑向應力大,線(xiàn)速度最高的輪緣周向應力最大[6];②工作過(guò)程的輪緣長(cháng)期為高溫拉伸狀態(tài),長(cháng)時(shí)使用后產(chǎn)生蠕變殘余變形;③隨發(fā)動(dòng)機啟動(dòng)—加速—最大—停車(chē)循環(huán),盤(pán)件上述拉伸的應力幅值呈周期變化,表現為疲勞載荷特征[7]。
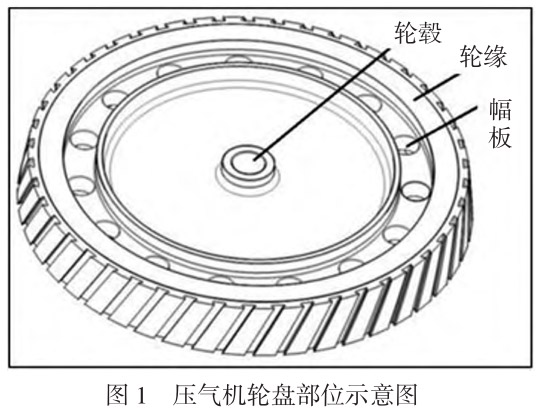
由于輪轂部位工作溫度較低(不超過(guò)200℃),輪緣部位溫度高達450℃~550℃[8],結合上述載荷分析可知,壓氣機盤(pán)的靜強度:輪轂部位的低溫(低于200℃)抗拉強度,幅板部位沿徑向中溫(約為350℃)抗拉強度,輪緣部位沿周向高溫抗拉強度(≥450℃)要求較高,避免上述部位在最高轉速下發(fā)生一次性大應力撕裂(瞬時(shí)斷裂)破壞。
輪緣部位尺寸大且易產(chǎn)生蠕變變形,故壓氣機盤(pán)輪緣部位的高溫(≥450℃)持久、蠕變強度要求加高,避免盤(pán)件長(cháng)時(shí)工作后的形狀、尺寸精度降低影響葉尖間隙,從而惡化壓氣機效率[9]。另外,壓氣機盤(pán)的幅板-輪緣轉接R處存在尺寸突變,易形成應力集中,因此盤(pán)部位的中溫(350℃)疲勞強度要求加高,避免幅板部位疲勞載荷作用下萌生疲勞裂紋,發(fā)生疲勞斷裂。
1.4取樣部位與項目
圖1為標準規定的TC11盤(pán)鍛件的顯微組織取樣圖,取樣位置為輪緣表面、輪緣芯部,幅板芯部,及輪轂芯部;力學(xué)性能取樣均來(lái)自輪緣部位。TC25、TC8-1盤(pán)鍛件力學(xué)性能的取樣部位參照TC11盤(pán)鍛件進(jìn)行。
由于TC11與TC8-1盤(pán)鍛件均采用等溫鍛造,TC25盤(pán)鍛件采用β鍛造。顯微組織應以追求盤(pán)鍛件的各區域的顯微組織均勻為目標,因此組織檢查應選擇輪緣、幅板、輪轂的典型部位,另外選取易形成組織缺陷的特殊部位進(jìn)行組織取樣檢查。
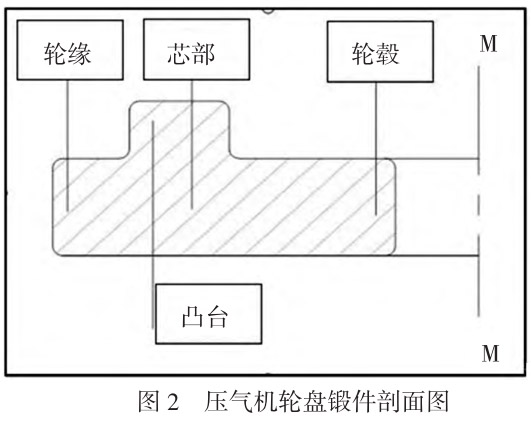
力學(xué)性能取樣應考慮典型部位承載特點(diǎn),測試該部位的力學(xué)性能。TC8-1盤(pán)鍛件檢驗的力學(xué)性能項目有:室溫拉伸,高溫拉伸,高溫持久,高溫蠕變,熱穩定性能,取樣部位為輪緣,沿周向選取,如表2所示[9]。
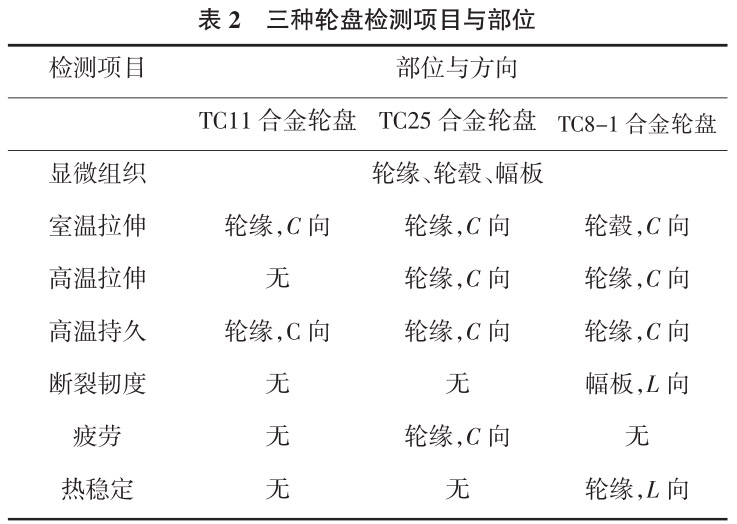
2、實(shí)驗結果
2.1顯微組織要求與測試結果
鍛件標準規定的組織級別與實(shí)際檢驗結果列于表3[10~12],具體組織形貌見(jiàn)圖3與圖4。
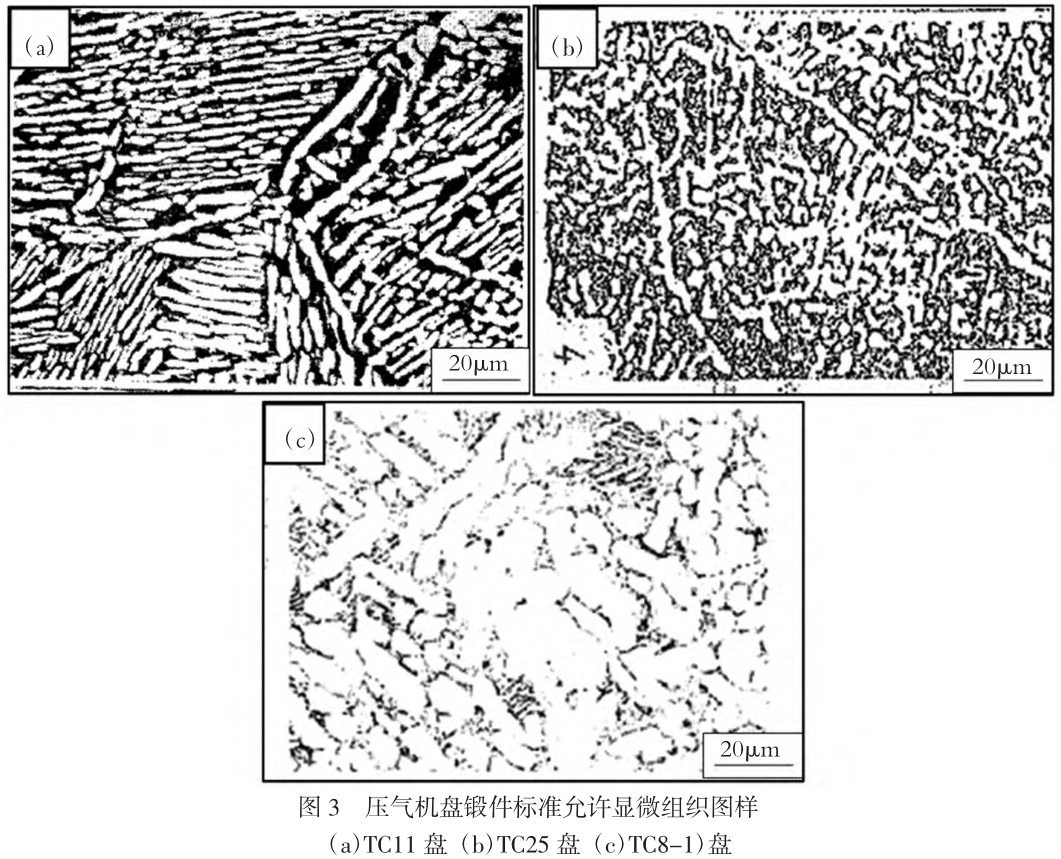

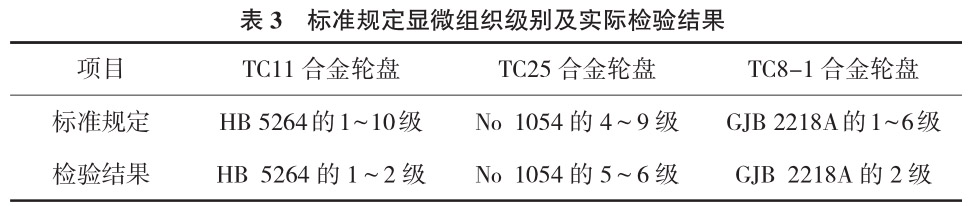
圖3a為片層狀魏氏組織:原始β晶界清晰可見(jiàn),且該部位析出連續α相,晶內α相與β轉相呈片層排列。魏氏組織的斷裂韌度值高但沖擊韌性差,抗疲勞性能最差[13]。壓氣機盤(pán)幅板與轉接R處應避免出現魏氏體組織。
圖3b為近似網(wǎng)籃組織:晶界析出連續α相,晶內α相與β轉相生長(cháng)方向呈片層排列,未編織成網(wǎng)籃??烧J為這是一種未充分網(wǎng)籃化的片層組織,而網(wǎng)籃組織的塑性、抗疲勞性能優(yōu)于片層組織。壓氣機盤(pán)幅板與轉接R處應避免出現魏氏體組織。
圖3c組織特點(diǎn)為α相呈現大塊狀、粒狀與蠕蟲(chóng)狀等不同形態(tài),來(lái)自GJB2218A《航空用鈦及鈦合金棒材和鍛坯規范》標準,組織形態(tài)可歸為大塊“蠕蟲(chóng)”狀α相夾雜著(zhù)β轉變組織的雙態(tài)組織,該組織在生產(chǎn)實(shí)踐中較罕見(jiàn)。
圖4a可見(jiàn),TC11盤(pán)鍛件組織均勻,初生α相再結晶進(jìn)行的較為完全,基本均呈圓滑的粒狀分布;β轉變組織含量適中,且內部可見(jiàn)片狀的次生α相與β相。此組織屬于典型的雙態(tài)狀組織,組織變形充分,總體而言,屬良好的鍛造組織。
圖4b的TC25盤(pán)鍛件為典型網(wǎng)籃狀組織:原始β晶界區域析出的初生α相呈彌散狀分布。形貌圓滑,鍛壓過(guò)程破碎充分。晶內α相與β轉相交互編織的網(wǎng)籃細小、齊整,屬于優(yōu)良的β鍛組織。圖4c的TC8-1盤(pán)鍛件顯微組織細小,均勻。α相已明顯的等軸化,不可見(jiàn)次生α相。屬變形充分的優(yōu)良等軸狀組織。
從上述顯微組織對比結果來(lái)看,輪盤(pán)鍛件變形充分,顯微組織均勻、細小,滿(mǎn)足標準要求。但應值得注意的是,圖3a與圖3c用來(lái)表征變形不充分的雙態(tài)組織是不恰當的。換言之,在α+β雙相區靠上部,小變形量條件下變形組織并非上述特征。
2.2力學(xué)性能要求與測試結果
鍛件標準對盤(pán)鍛件的室溫力學(xué)性能要求以及盤(pán)鍛件的實(shí)測數據列于表4,熱穩定性能列于表5。
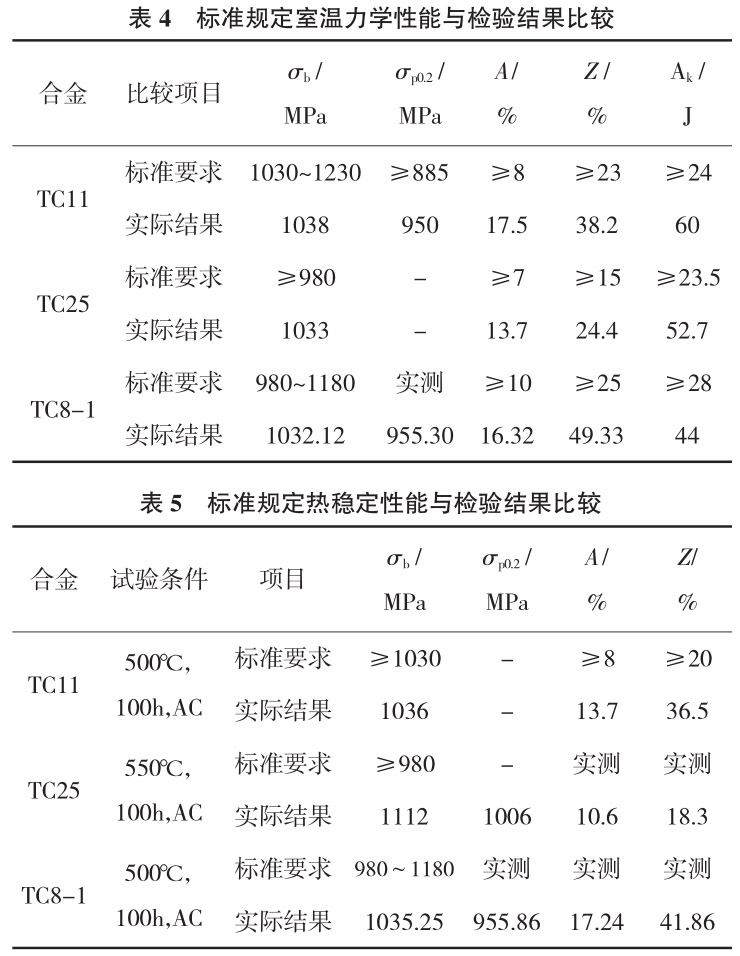
從表4可見(jiàn),三種合金的盤(pán)鍛件力學(xué)性能較之標準規定數值均有較大的裕度。TC25合金塑性指標尤其是斷面收縮率Z較之TC11與TC8-1合金合金明顯偏小,這符合網(wǎng)籃組織塑性低于等軸組織的特性。
從表5來(lái)看,TC8-1與TC25合金的抗熱損傷性能優(yōu)異,較之室溫拉伸試驗結果相差不大,說(shuō)明三種合金均適合作為高溫長(cháng)時(shí)承載件使用,符合熱強鈦合金的性能特征。
3、分析與討論
從成分特點(diǎn)可看出,TC25合金較之TC11合金的[Al]更高,接近α+β雙相鈦合金的成分極限,且TC25合金含少量共析型β相穩定元素W,因此TC25合金熱強性能更好,符合高溫高強鈦合金的成分特點(diǎn)[4]。而TC8-1合金較之TC11合金適當增加了Mo含量,降低Si元素含量,并以Sn替代部分的Al元素。[Mo]決定馬氏體鈦合金的相變強化效果;長(cháng)時(shí)使用后鈦合金析出的硅化物導致合金脆化[5],調整Si含量可抑制此不利影響。故TC8-1合金適合作為高強,長(cháng)壽命壓氣機盤(pán)使用。
分析三種合金輪盤(pán)的顯微組織,TC11與TC25盤(pán)的輪緣、幅板與輪轂屬于不同變形量的區域,故進(jìn)行顯微組織檢查以驗證鍛造工藝參數的正常性。但值得注意的是,靠近輪緣外部的顯微組織檢查為鍛造組織缺陷檢查,因為在盤(pán)件模鍛過(guò)程,根據鍛造“X理論”[8],輪緣外部屬于小形變量區域,容易形成晶界初生α相連續,原始β晶粒粗大等形變不足導致的組織缺陷,應加強對此區域的顯微組織檢查。
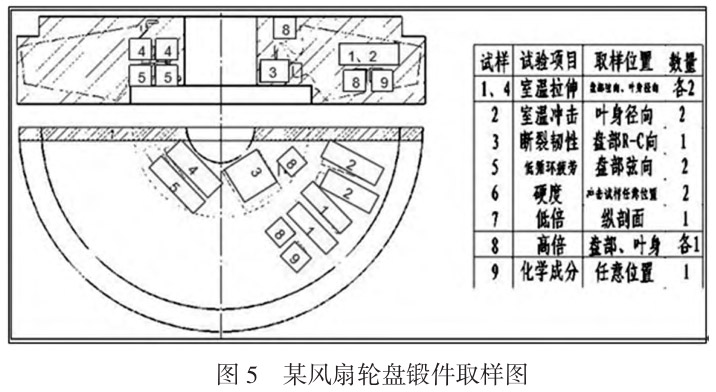
從力學(xué)性能取樣來(lái)看,輪緣部位長(cháng)時(shí)在高溫下處于兩向拉伸狀態(tài),對高溫持久性能、熱穩定性要求高。但應注意,疲勞失效也是盤(pán)類(lèi)零件較普遍的一種失效方式[9],有必要在幅板部位沿周向檢測疲勞性能。實(shí)際取樣過(guò)程中,由于疲勞試樣尺寸較長(cháng)(?6mm×90mm,夾持處螺紋M12),幅板部位弦長(cháng)較短,難以滿(mǎn)足取樣要求,故多數情況下從輪緣取樣進(jìn)行代替。
另外,在幅板部位測試斷裂韌度KIC,也是一項常見(jiàn)的取樣要求,國內某渦扇發(fā)動(dòng)機用TC17鈦合金盤(pán)鍛件即有此項要求。斷裂韌度KIC表征材料在高應力作用下抵御斷裂的能力,取決于強度與塑性的匹配[11],屬靜強度范疇??蛊谛阅鼙碚鞑牧显谥芷趹ψ饔孟碌钟鶖嗔涯芰?,屬疲勞強度范疇。只有循環(huán)周次極少的疲勞破壞,才與斷裂韌度近似。二者不可一概而論,以片層魏氏組織為例,KIC值高但抗疲勞性能差。
以目前國內某大流道渦扇發(fā)動(dòng)機整體風(fēng)扇葉盤(pán)的力學(xué)性能取樣圖[12](圖4)為例,沿盤(pán)輪緣弦向檢驗抗疲勞性能,輪緣徑向或弦向檢驗KIC值,室溫拉伸試樣取自葉身徑向(葉片離心載荷所致)與盤(pán)周向(此載荷亦誘發(fā)疲勞源)??梢?jiàn),該鍛件的取樣圖最為完備合理,符合以上推論。
從力學(xué)性能來(lái)看,等軸α相的尺寸與體積分數,次生α相厚度,α相與β相的組織形態(tài)等均對力學(xué)性能構成影響。初生等軸α相體積分數高則塑性、韌性升高,而片層組織(次生α相+β轉相)體積分數高則塑性、韌性降低而斷裂韌度升高。次生α相是高溫下的強化相,其含量影響合金高溫拉伸與高溫持久強度。
拉伸應力作用下,晶界α相內位錯發(fā)生滑移,對于TC25盤(pán)的網(wǎng)籃狀組織而言,其原始β晶粒較粗大,故晶界α相相對含量少,難以協(xié)調變形[17],因此網(wǎng)籃組織塑性遜于等軸組織,但高溫持久、蠕變強度優(yōu)異。
高溫強度取決于次生α含量與尺寸,TC25盤(pán)屬于網(wǎng)籃狀組織,該組織的α相與β相相互交錯編織,高溫下不易滑動(dòng),熱損傷效應較小。TC8-1合金屬于高[Mo]、低Si含量合金,長(cháng)時(shí)在高溫暴露后Ti5Si3脆性相析出受到抑制,故熱穩定性能優(yōu)異。
4、結論
通過(guò)TC11,TC25,TC8-1鈦合金制發(fā)動(dòng)機壓氣機盤(pán)的標準與實(shí)物對比,并參照TC17鈦合金制壓氣機盤(pán)鍛件標準,形成結論如下:
(1)顯微組織需選取典型變形部位檢測,三種鈦合金盤(pán)鍛件選取輪緣、幅板、輪轂部位,符合鍛件的變形特征。
(2)三種鈦合金盤(pán)鍛件變形充分,顯微組織均勻、細小,均滿(mǎn)足標準規定。但TC11合金、TC8-1合金輪盤(pán)標準引用的顯微組織級別與圖片不夠科學(xué)。
(3)壓氣機盤(pán)的輪緣部位對高溫拉伸、蠕變性能要求較高;幅板部位對中溫抗疲勞性能要求高;輪轂部位對低溫拉伸強度要求較高。
(4)對照輪盤(pán)部位—性能項目關(guān)系,三種鈦合金盤(pán)鍛件標準規定的力學(xué)性能檢驗項目存在少量缺失。另外,可取消輪盤(pán)檢熱穩定性能。
(5)實(shí)際盤(pán)件的顯微組織、力學(xué)性能較之標準規定數值均有較大的裕度。說(shuō)明目前三種鈦合金盤(pán)鍛造工藝相對成熟??蛇m當提高標準要求,嚴格鍛件質(zhì)量控制。
參考文獻:
[1]O.П.索朗寧娜,C.Γ.鉻拉祖諾夫著(zhù),張志方,葛志明譯.熱強鈦合金[M].北京:第三機械工業(yè)部第六二一研究所,1978.
[2]中國航空材料手冊編輯委員會(huì ).航空材料手冊[M].北京:中國標準出版社,2002.
[3]魏壽庸,何瑜,王青江.俄航空發(fā)動(dòng)機用高溫鈦合金發(fā)展綜述[J].航空發(fā)動(dòng)機,2005,31(1):52-58.
[4]蔡建明,郝孟一,李學(xué)明,等.BT36高溫鈦合金的成分特點(diǎn)及組織研究[J].材料工程,2000(2):10-14.
[5]錢(qián)九紅.航空航天用新型鈦合金的研究發(fā)展及應用[J].稀有金屬,2000,24(5):218-223.
[6]陳光.航空燃氣渦輪發(fā)動(dòng)機結構設計[M].北京:北京航空航天大學(xué)出版社,1988.
[7]中華人民工業(yè)國航空航天工業(yè)部.HB5263TC11鈦合金壓氣機盤(pán)模鍛件[B]1995.
[8]《透平機械現代制造技術(shù)叢書(shū)》編委會(huì ).葉片制造技術(shù)[M].北京:科學(xué)出版社,2002.
[9]張棟.機械失效的痕跡分析[M].北京:國防工業(yè)出版社,1996.
[10]XX10發(fā)動(dòng)機冶金型號標準編制委員會(huì ).Q/S10.0535-2004TC17鈦合金壓氣機盤(pán)鍛件[B].2004.
[11]馬少俊,吳學(xué)仁,劉建中.TC21鈦合金的顯微組織對力學(xué)性能的影響[J].航空材料學(xué)報,2006,26(5):22-27.
[12]XX20發(fā)動(dòng)機冶金型號標準編制委員會(huì ).Q/S20.2303-2010TC4鈦合金整體風(fēng)扇輪盤(pán)鍛件[B].2010.
[13]國防科技工業(yè)委員會(huì ).GJB2218A-2008航空用鈦及鈦合金棒材和鍛坯規范[B]2008.
[14]全蘇國家標準委員會(huì )著(zhù),王金友譯.NO1954鈦合金的金相分析[M]北京:中國航空工業(yè)總公司北京航空材料研究院,1976.
[15]中華人民工業(yè)國航空航天工業(yè)部.HB5264TC11鈦合金盤(pán)及其餅坯金相組織標準[B]1983.
[16]瓦利金И.莫依謝耶夫著(zhù),黃寶明,張勝,郭德倫,譯.鈦合金在俄羅斯飛機及航空航天上的應用[M].北京:航空工業(yè)出版社,2008.
[17]朱景川,何東,楊夏緯.TA15鈦合金雙重熱處理工藝及其組織演化的EBSD研究[J].稀有金屬材料與工程,2013,42(2):382-387.
相關(guān)鏈接